IoTやデジタルツールの導入など、工場のデジタル化は生産効率を飛躍的に向上させる大きなチャンスだと言われる。とはいえ中小規模の町工場では設備や人材、コストなどのリソースが限られるため、デジタル化を成功させるまでのハードルは高い。そうした中、複数の中小企業がつながることで、その困難を乗り越えたユニットがある。東京都足立区と江戸川区で同じ板金業を営む3社による「東京町工場 ものづくりのワ」だ。3社のITシステムを先導する今野製作所の今野浩好代表取締役は、このプロジェクトを「協働」というキーワードで解説する。複数の工場がつながることとデジタル化のメリットとは何だったのか。
参加企業/メンバー プロフィール
今野製作所
ステンレスの加工製造に特化しており、主なクライアントは理化学業界。大学や企業の研究所などで使用される機材の骨組みや部品をオーダーメイドで製作する。東京都足立区の板金工場のほか、大阪に営業所、福島に油圧機器製造工場を持つ。
西川精機製作所
産業設備用の治工具や医科学研究機器などを中心に製造。スーパーコンピュータ「京」の基盤を表面処理した際の特殊治具などを製作したこともあり、個別対応での設計製作に力を入れる。純国産アーチェリーなど、アイデア力を生かした事業開発にも挑戦する。
エー・アイ・エス
得意とするのは、箱物筐体(きょうたい)。都内では珍しい大型クレーンの設備を備えており、大型製品にも対応する。マンションの室外機カバーや飛行場の管制塔の管制卓など、案件ごとの個別設計で製造を行う。
町工場に共通する問題――「協働」によって見えた解決の糸口
――「東京町工場 ものづくりのワ」(以後「ものづくりのワ」)について教えてください。
今野:板金(金属の加工製造)を基幹事業とする町工場3社によるユニットです。
2013年に発足し、デジタル化によるものづくりや業務改善を3社で協力して進めています。私たちの関係性は極めてフラットであり、幹事企業は存在しません。同じ板金屋でもそれぞれ異なるノウハウを培ってきており、設備も顧客もまったく違う、いわゆる同業異分野です。各社が持つ強みを活かして協力し合い、競争力を上げるというのがコンセプトで、「協働」という考え方のもとで進めてきました。
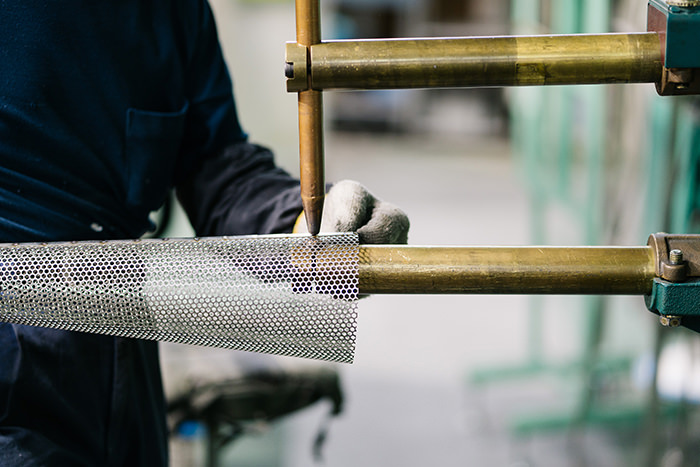
――発足のきっかけについて教えてください。もともと3社はどういった課題を抱えていたのでしょうか。
今野:私たちにはもともと仕事でのつながりはなく、経営者交流会で知り合いました。意気投合して頻繁に3人で会うようになり、お互い本音を出し合って意見交換する中で、3社で共通の課題があることが分かりました。
最も大きな課題は生産性の向上でした。町工場の仕事は非常に属人的になりがちで、従業員の中で豊富な経験と高い判断力を持つ人物が「キーマン」となり、顧客対応から現場のさい配までのすべてを担うことが多いのです。このやり方でも、特定の顧客との取引だけであれば特に問題はないでしょう。しかし顧客の多くが海外の事業者に流れている昨今、私たちのような町工場が競争力を高めていくには、新規顧客の開拓や、高収益が見込める設計要素の濃い案件を積極的に進めていくことが不可欠です。こうした案件は複雑で、品質の要求水準が高いため、これまでのやり方でキーマンだけに頼っていては人的リソース不足に陥ります。
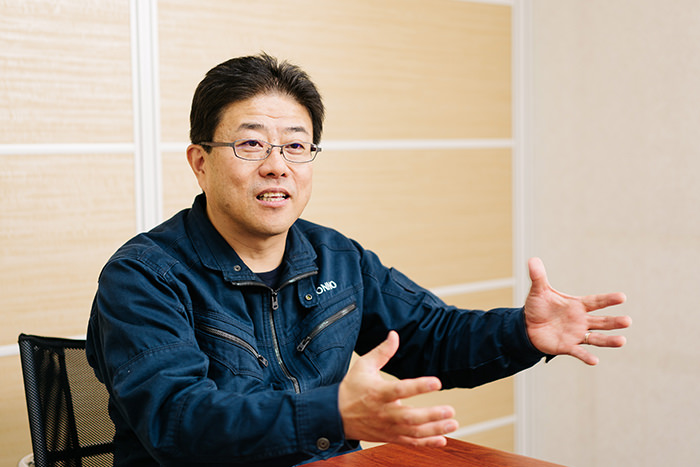
今野:弊社では「ものづくりのワ」を結成する前の2010年から、現在はIVI(Industrial Value Chain Initiative) 理事長でもある法政大学の西岡靖之教授のアドバイスを受けて、社内の生産管理のIT化を推進していました。これを会社の垣根を越えて3社合同でやろうと提案したのが、「ものづくりのワ」の始まりです。
関連記事
IoT導入、「ゆるやかな標準」づくり――IVIが考える、日本のものづくりのアップデートとは
デジタル化による業務改善で付加価値を効率的に生み出す
――具体的にはどのような連携を行うことで、キーマンへの依存度の高さを改善したのでしょうか?
今野:「協働受注」のシステムです。共同体としての受注とは異なり、工程の水平連携によって職人の知恵や経験などのノウハウと、設備などのリソースをシェアするのです。昔はキーマンが図面を持って他社を訪ね、技術や製造方法に関する意見交換を行い、他社に仕事を依頼することがありました。これは横のつながりを持つ町工場ならではの強みであり、ものづくりのアイデアの根源となるものです。まずはこれをデジタルの世界で行おうと考えました。
具体的には、サイボウズの業務改善プラットフォーム「kintone」を使って、顧客からの見積もり依頼が入ると、依頼を受けた会社がその内容をkintoneのデータベースに登録するようにしました。
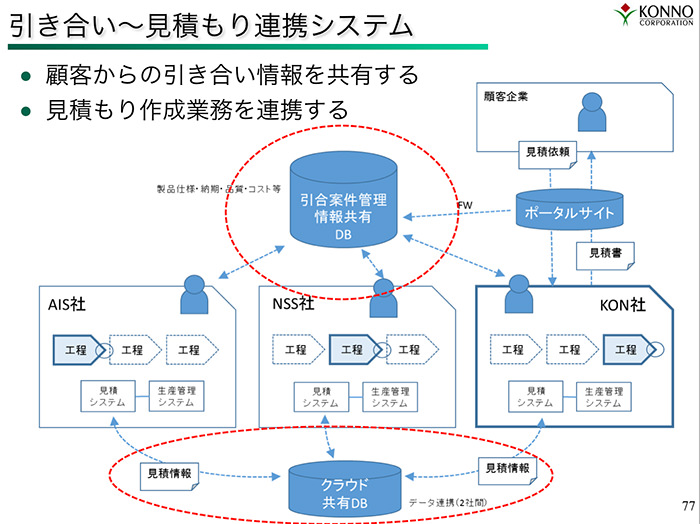
今野:情報はすぐに3社に共有され、各社のキーマンたちはその画面を見ながら、画面のすぐ横にあるSNSのような機能でコメントをやりとりできます。これにより、やりとりの記録がノウハウの集積としてデータで残るため、類似の案件が発生した際に参照できます。事例が増えるほどに仕事がスムーズになっていきました。
――他にも成果を出した取り組みはありますか。
今野:「ものづくりのワ」の発足を決めた時、外部からの協力を要請しました。ITコーディネータ協会、バリューチェーンプロセス協議会、法政大学デザイン工学部西岡研究室、東京都中小企業振興公社に参画いただき、2014年8月から20カ月間にわたり、「ITカイゼン・情報連携部会」「業務プロセス・ルール部会」「ビジネスモデル部会」の3つの部会を立てて活動しました。
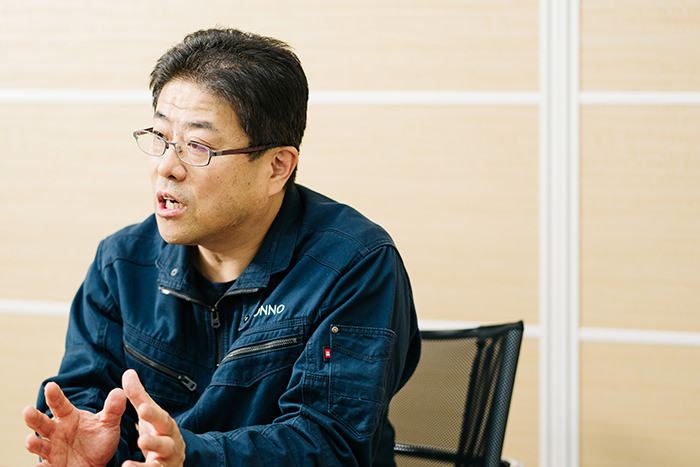
今野:ITカイゼン・情報連携部会では、工場の中の業務を一つずつひも解きながらIT化していきました。特に成果が出たのが、「コンテキサー」と呼ばれる業務アプリケーション開発ツールです。生産管理における情報を整理整頓し、業務の流れを可視化して共有することができました。例えば発注作業であれば日付、発注先、数量などといった情報がデータで伝達されます。かつては帳票も統一されておらず、キーマンがファックスで発注していたので、詳細な内容を把握しているのは作業者のみです。コンテキサーを使ったシステムから発注すれば、情報はすべてデータとして記録され、部署や会社をまたいだ共有が可能になりました。
IT化と同時進行での業務改善で、リアルタイムの検証が可能に
――デジタル化にあたっての業務プロセス見直しとして、どのようなことをされましたか。
今野:業務プロセス・ルール部会では、コンサルティング専門家の指導を受けながら業務の流れを整理していきました。それまで経験則で進めていた業務を定義づけていき、続いて各プロセスにおける課題を洗い出したのです。3社から出た個別課題、合計87件を統合して横並びの1つの表にしたところ、社内への情報展開や現場の状況整理に関する37件が共通課題であることがわかりました。中でも特に優先課題としてピックアップした「工程別の進捗管理」「発注情報の共有」などの14件を改善していくことにしたのです。
――その見直しをどのようにしてデジタル化に活かしていったのでしょうか。
今野:通常であれば、業務分析を実施した上でIT化に着手するのがセオリーですが、私たちはあえて同時進行で行いました。IT改善のテンプレートシステムを実装して運用しながら、業務改善によって洗い出された問題点を順次そこに反映させ、使いにくい部分があれば修正していくという方法で進めました。
3社の中でも特にエー・アイ・エスさんは目に見える変化がありました。工程進捗管理のシステムをフル活用するために現場のいたるところにモニターを設置して、次に行うべき受注が画面に表示されるようにしたのです。以前は生産システムが存在しなかったため、前工程は余力があるのに後工程は忙しくなったり、着手順の判断を誤って出荷時間間際に納期に追われることになったりと、現場が混乱することが多かった。それが進捗管理を可視化することでこれらの問題はなくなったので、現場のコミュニケーションが活発になり、社内の雰囲気が変わりました。
職人の技術をITで数値化し、効率的な技能継承を
――20カ月間の取り組みを終え、新たに見えてきた課題はありますか。
今野:部会の活動は終わりましたが、「ものづくりのワ」の活動は、工程進捗や見積もりなど、毎年テーマを変えて改善活動を進めています。今年度の2本柱は「デジタルものづくり」と「溶接技術の研究」。デジタルものづくりとは、3次元CADシステム(コンピュータによる設計支援ツール)や曲げ加工シミュレーションなど、各社が備えるリソースのシェアです。
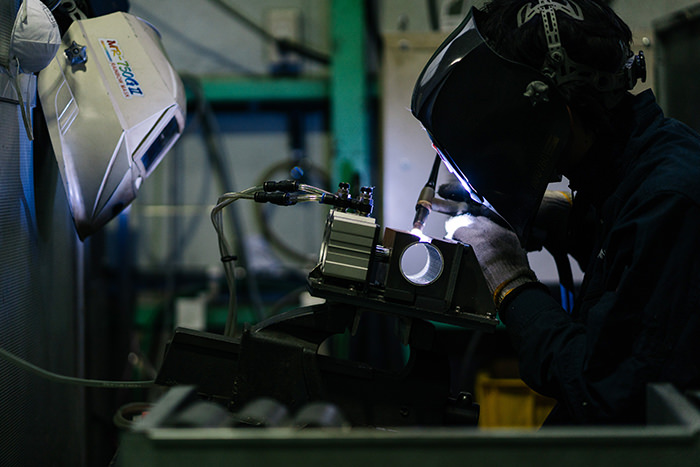
今野:溶接技術の研究については、「ものづくりのワ」の事務局長をしている溶接の専門家で、「Creative Works」代表の宮本卓さんが中心になった「溶接技術者養成IoTブース」の構想があります。このIoTブースとは、熟練の職人による溶接作業をカメラで撮影し、姿勢や動作を記録するとともに、温度センサーや電流センサーで加工条件や状態をモニタリング。そして溶接トーチの動きをモーションセンサーでトレースして、熟達した作業者とそうでない人の差異を可視化できるようにする。学習者はそれを見ながら、改善課題を知ることができる仕組みです。溶接は高い技能を要する作業であり、私たちにとって人材の育成は引き続き最も大きな課題。「職人の勘を身につけるには10年の修行が必要だ」とよく言われますが、現在の目標は3年で一人前の職人が育つシステムを作りたい。
――こうして培った企業間連携のモデルを他社に展開するために、どのような活動をされていますか。
今野:2015年にIVIが発足された際には3社そろって参加し、私たちの活動を工程進捗管理の実例としてモデル化してIVIのワーキング・グループで共有しました。今年はIVIのプロジェクトメンバーとして、私たち3社を含めた首都圏の企業5社が集まる「東京町工場チーム」と、静岡県内の中小企業による「SPメディカルクラスタチーム」が連携し、知的財産の継承という観点からのIT化を推進しています。参加企業がそれぞれに行っている取り組みを事例として持ち寄り、さらに大きな枠組みにおいての連携の仕組みを構築するのが狙いです。こうして町工場が手を取り合い、経験値をシェアしていくことで、ものづくりの現場がスピーディに発展していけばと願っています。
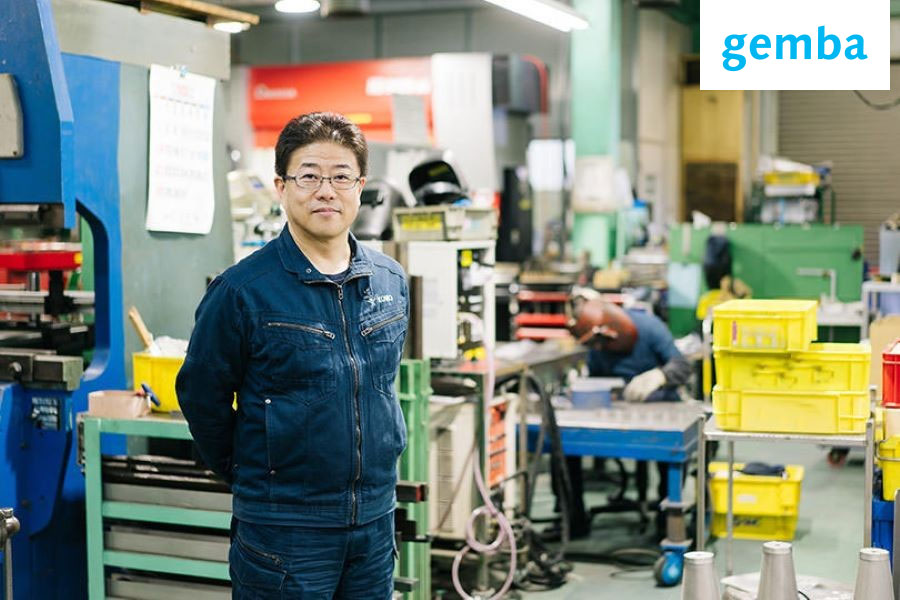