地方の町工場の事業承継をした3代目社長が、事業モデルを大きく転換し、画期的な技術を開発した。たった2時間半で樹脂成形金型の製作を実現する「デジタルモールド」だ。この技術は自動車業界や家電業界など、名だたる日本国内メーカーを驚かせ、経済産業省「2019年版ものづくり白書」のトップにも事例として掲載されている。この画期的な技術を採用したビジネスを作り上げたのは、のどかな風景が広がる長野県伊那市に本社を構える「有限会社スワニー」の橋爪良博代表取締役だ。事業の転換を成し遂げたその背景と、日本のものづくりに対する思いを聞いた。
借金を乗り越え、新サービスで唯一無二の企業へ
――橋爪社長は、「有限会社スワニー」の3代目社長として事業承継をされました。まずは、会社を継いだ当時のことを教えてください。
橋爪:スワニーがビジネスを展開している長野県伊那市は、元来電子部品や精密機械などの製造業が盛んな土地です。祖父が1970年に創業した「有限会社スワニー」もマイクロモーターやコンデンサーを製造していました。
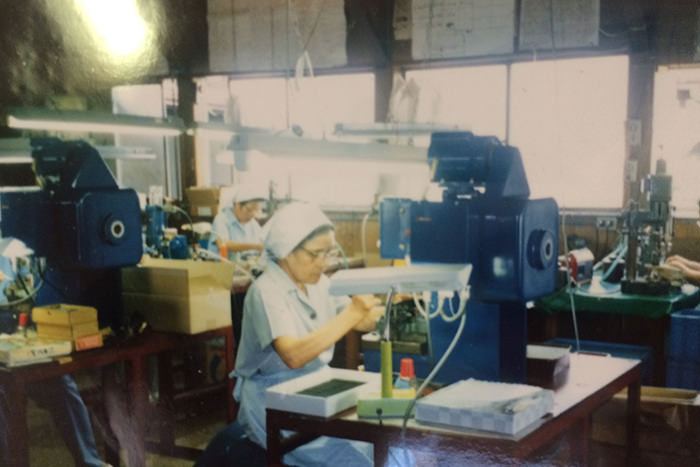
しかし発注元となる日本のメーカーが、工場などの生産拠点を海外へ移転する動きが加速する中で、仕事も売り上げも従業員も失いました。製造業で働くサラリーマンだった僕が、2010年にスワニーを父から継いだ時には、数千万円の借金だけがありました。
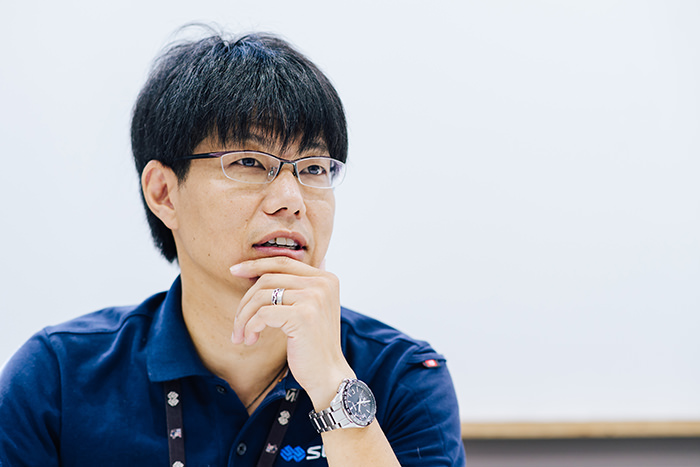
潤沢な資金があるわけではない。だからこそ他社と同じことをやっていては浮上できません。この9年間、とにかく新しいビジネスを作ることに注力してきました。浮上のきっかけとなったのは、3Dプリンタでした。
多品種少量生産の時代に適した「デジタルモールド」の誕生
――どんな経緯で3Dプリンタに着目されたのでしょうか?
橋爪:事業を継いだ当時、プラスチックや金属の製品を量産する際は、金型での製造がほとんどでした。一度金型さえ作ってしまえば、材料を溶かして流し込むだけで大量のものが作れるからです。しかし一方で、金型自体の製作費が高額で、しかも複雑な技術が求められるため製作期間が長くなってしまうというデメリットもありました。
例えば1,000円の製品を500個販売し、売上50万円を目指したくても、部品の金型だけで170万円ほどの製作費と1カ月の時間がかかるのです。これでは採算があわず、新しい製品を作る際には、金型をつかっても採算がとれるものという制限が生まれてしまっていました。
橋爪:つまり、売れるかどうかわからない製品でも、大量生産を前提に作る必要があり、企業にとっての障壁になっていました。特に、資金が限られている場合や、小ロットやマスカスタマイゼーションなど市況にマッチするビジネスを狙う中小企業やベンチャー企業にとっては、新規の製品開発に二の足を踏まざるをえないでしょう。実際、製品開発においては、量産(製品化)の前には高い壁がある、と言われています。
また当時のお客さまからは、「新しいものをつくるために、試作をもっと簡単にできるようにしたい」という声もお聞きしていました。
こうした課題を解決するために3Dプリンタを活用できるのではないか、と考えたのです。
――低コストでの少量生産や試作ができず、新規開発に制限が生まれていたのですね。どのように解決したのでしょうか。
橋爪:当時も3Dプリンタ自体で試作や少量生産を行うという動きはありました。しかしながら3Dプリンタで造形した部品は高額で、材料も実際の製品とは異なるため、活用には制約があります。 そこで発想を転換し、3Dプリンタで従来の金属製の金型に代わる「樹脂型」を製造する「デジタルモールド」という技術を生み出しました。この3Dプリント樹脂型「デジタルモールド」をツールとして活用すれば、プラスチック成形・金属プレスなど、量産品と同じ材料・加工方法で部品の試作をしたい、少量製品生産の金型イニシャル費用を削減したい、といった要望に応えることができます。デジタルモールドの製作費は数万〜数十万円で、寸法や形状にもよりますが2時間半ほどで型ができあがります。
つまり、このデジタルモールドを従来の金型の試作として使うことで、課題であったコストや長い開発期間を大幅に削減することができるというメリットがあるのです。

橋爪:一般的に型に樹脂材料を流し込んで成形する際には、高い圧力がかかるため、型にはそれなりの強度が必要です。一般的なアクリルやプラスチックといった樹脂ではその力に耐えきれず割れてしまいますが、3Dプリンタと専用材料で製作されたデジタルモールドは、表面層には硬度と耐熱性が高い素材、内部には靭性(じんせい)のある素材を使っているため、成形時の熱や圧力に耐え、金型として使用できるのです。
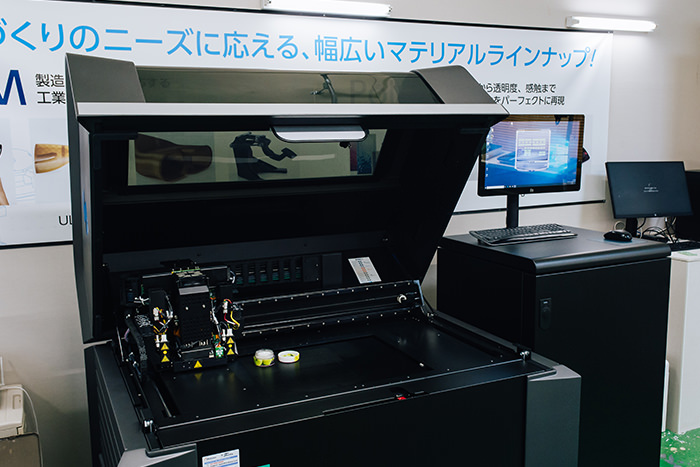
橋爪:開発期間については、例えば数百個から千個程度の小ロットであれば、企画から量産まで最短6日で完了することができます。従来ならデザイン、試作、金型設計を経て量産が完了するまでに数カ月から数年が必要でした。かつ人件費なども含めると数百万円のコストがかかっていたので、革新的だと言えるでしょう。
とにかく試作のスピードを驚異的に速められるのがデジタルモールドの最大の特徴です。この技術を活用することでアイデアを実現しやすくなり、どんどん新しい製品が世の中に生まれればよい、と思っています。
デジタルモールドは現在、自動車メーカーや家電メーカーといった企業の方々に多く使っていただいています。また海外からもお客様が来てくださいます。スワニーは、長野県伊那市という地方にある社員15名の小規模な会社ですが、遠方からわざわざここに足を運んでいただけるだけの、魅力と価値のあるアプリケーションを作り上げられたと確信しています。
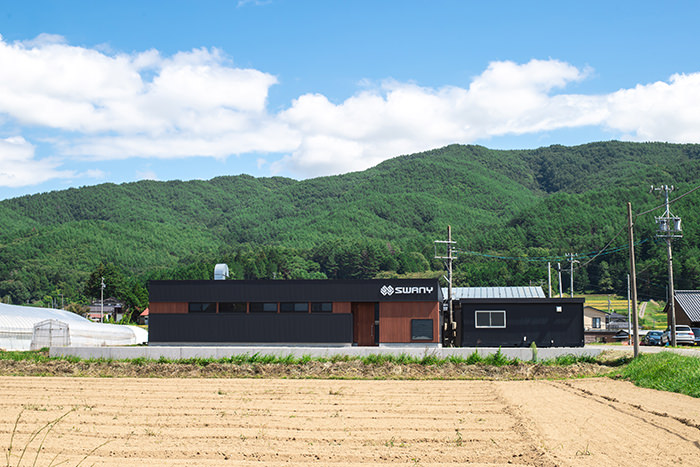
失敗しやすい環境だからこそ生まれた「ハイブリッドモールド」
――画期的なデジタルモールドなどの技術は、どのようにして生まれたのでしょうか。
橋爪:冒頭で、新しいビジネスを作ることに注力してきたと申し上げましたが、会社を継いだ2010年に決めた理念が、「失敗をしてもいいから、スピーディーに挑戦を繰り返す」です。まず、スピードを上げるために分業はせず、1人の設計者が一気通貫ですべてを担当するようにしました。設計から、型を作って成形するまで、さらにお客様との打ち合わせも見積り提出も、すべてです。切削機や3D CADなども同じ担当者がすべて操作します。そのような環境で、3Dデータと生産技術力を駆使して、アイデアを素早く形にする会社、というコンセプトが次第にできていきました。
もう1つ、失敗してもいい環境を作るためのルールも設定しました。「仕事がない時は、社内の機械と材料を自由に使って遊んでいい」というものです。その代わり、作ったモノはスワニーのブログにアップしてもらいます。Facebookにもリンクしていて、「いいね」の数×100円が、「いいね手当」として社員の給与に入るので、ちょっとしたインセンティブとしても機能しています。
なぜこんなことをするのかというと、1つには、会社が導入する新しい機械や技術を、積極的に経験してほしいからです。自分のアイデアを自分で形にすると、モチベーションも上がりますよね。もう1つは、社内のよいアイデアの種を社内の価値観でつぶしてしまわないためです。
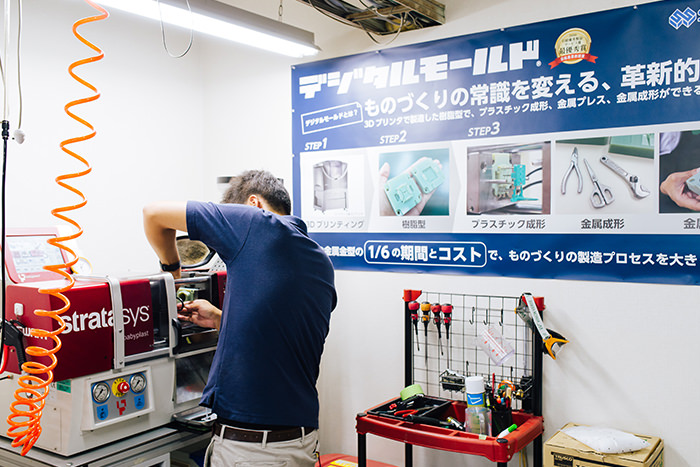
橋爪:ある日、「いいね手当」で、アルミブロックを買ってきた社員がいました。切削機の使い方を覚えたので、アルミで金型を彫ってみたい、と。僕はもともと金型のプロなので、彼女に対して「失敗してもいいけど、素人がすぐに作れるものじゃないよ」と言いました。するとしばらくして、本当にアルミの金型ができたんです。まさに僕自身が社内で社内のよいアイデアをつぶしていたな、と反省しました。
この社員のノウハウをデジタルモールドに組み合わせ、2017年には「ハイブリッドモールド」という技術の提供をはじめました。デジタルモールドに加えて、金型のベース部分をアルミ型にすることでより耐久性を向上させ、それまでよりも大きなロットでの量産を可能にした金型です。数千個までであれば、この技術で量産も可能になりました。
社員たちは、遊びながら画期的な技術を生み出してくれています。すごいスピードで目から鱗が落ちるようなサービスができていくのは、失敗できる環境のおかげです。
挑戦の妨げになる「壁」を排除し、製造業にイノベーションを
――スワニーは、経済産業省が後押しする「スタートアップファクトリー構築事業」でスタートアップを支援するための拠点として選ばれていますね。
橋爪:はい。量産化試作ならスワニーに相談すれば解決する、ということでスタートアップのお手伝いをさせていただいています。まず試作してみる、少量作って実証実験をしてみる。そんな時に、安く短時間でできるデジタルモールドは最適です。最後までスピード感を失わず、よいアイデアを形にして、日本から世界中で売るための仕組みができたらという思いで、全面協力しています。
現在の日本には、開発やプロトタイプを出す人はたくさんいて、量産してくれる工場も山ほどあります。でもその中間部分である量産化試作には「壁」があるのです。
スタートアップが新商品を工場で製造したい場合、実際にものができるまでには設計屋、金型屋、電気で動く商品だったら基盤屋など、約20社を回り、技術や費用を検討しなければなりません。さらに原価、商標、特許、PSE(電気用品安全法)試験なども考慮せねばならず、製品化までに2〜3年はかかってしまうんです。よいアイデアなのに、形にならず途中で止まってしまっているということも多い。もっと製品化の速度を上げていかないと、日本からよいものは生まれません。
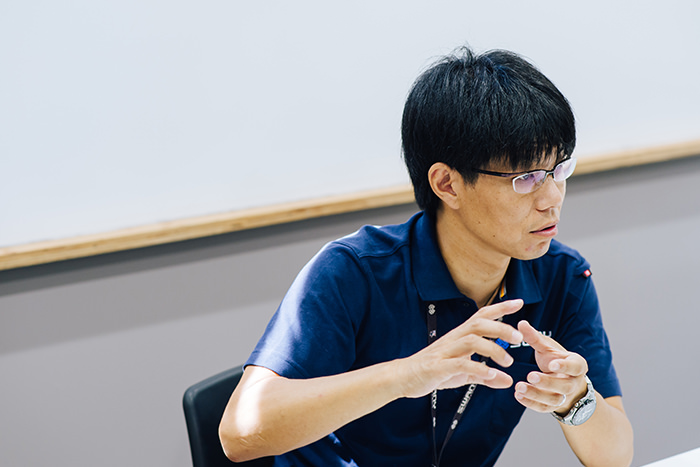
――最後に、今後の目標について教えて下さい。
橋爪:3D CADも3Dプリンタも、ソフトウェアやシステムはあくまで手段(ツール)にすぎません。重要なのは「何を実現したいのか」ということです。お客様に期待以上のサプライズができる、提案力と実現力。それが大切です。「日本で一番頼ってもらえる設計会社を目指す」、これが、この会社を継いだ時から現在まで、ずっと変わらない目標です。
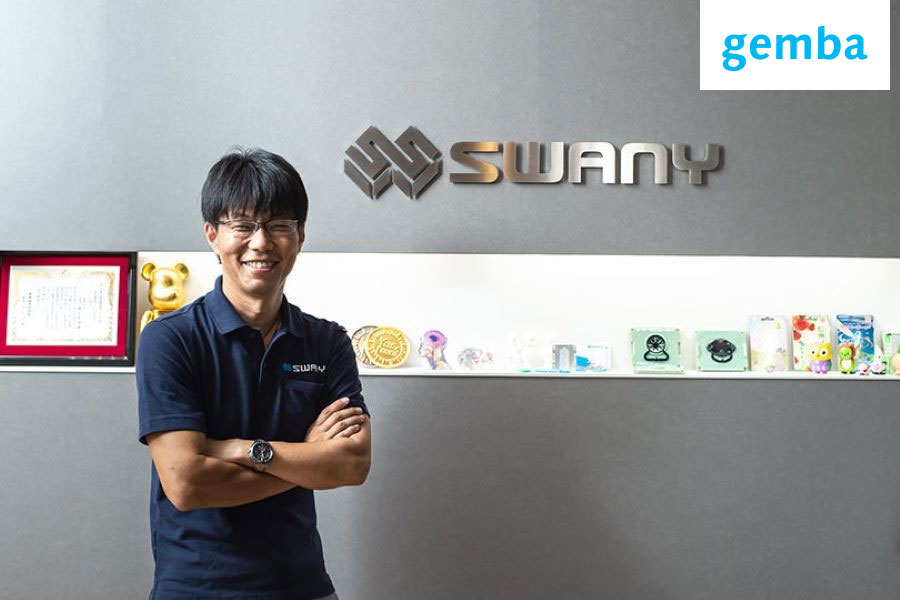