「日進工具株式会社」は、超微細加工に欠かせない切削工具「超硬小径エンドミル」の製造販売で国内トップシェアを誇るメーカーだ。“髪の毛に文字が彫れる”精度を持つ刃先径0.01mmの「マイクロエッジ」を始め、数々の「見えない世界の切削工具」を作り出してきた。デジタル家電や通信機器、自動車などに使用される電子部品やデバイスの超小型化・高集積化・薄型化が加速するなか、それらを作るための金型や各種部品はより精密・微細の方向へ技術進歩している。日進工具は超硬小径エンドミルの将来性を早くから予測し、成長を遂げてきた。いま精密・微細加工の未来をどう見据え、切り拓こうとしているのか。後藤弘治代表取締役社長に話を伺った。
髪の毛にも文字が彫れる! 技術進展にあわせて需要が高まる「超硬小径エンドミル」とは
――まずは日進工具がどんな会社なのか教えてください
後藤:創業は1954年で、父と祖父、社員1人のわずか3人の工場からスタートしました。当時は鉛筆削り用のカッターなどを作っていましたが、80年ごろに超硬合金が登場したことにより、超硬エンドミルのメーカーとして成長することができました。
――「エンドミル」とは、どのような切削工具なのでしょうか。
後藤:「エンドミル」はマシニングセンタ(数値制御工作機械)に取り付け、金型や部品などの切削を行う工具で、見た目は鉛筆に似た金属の棒です。そのなかでも、素材に超硬合金を使用した刃先径6㎜以下のエンドミルが「超硬小径エンドミル」です。
当社が製造している最も細い製品は、刃先径0.01mmの超微細加工用エンドミル「マイクロエッジ」です。構想から8年かけて2005年に完成しました。常に在庫を持つ標準品として販売しているのは当社だけで、0.01mmの精度を世の中に広くわかりやすく伝えるために、“髪の毛に文字が彫れる”ことをキャッチコピーにしています。
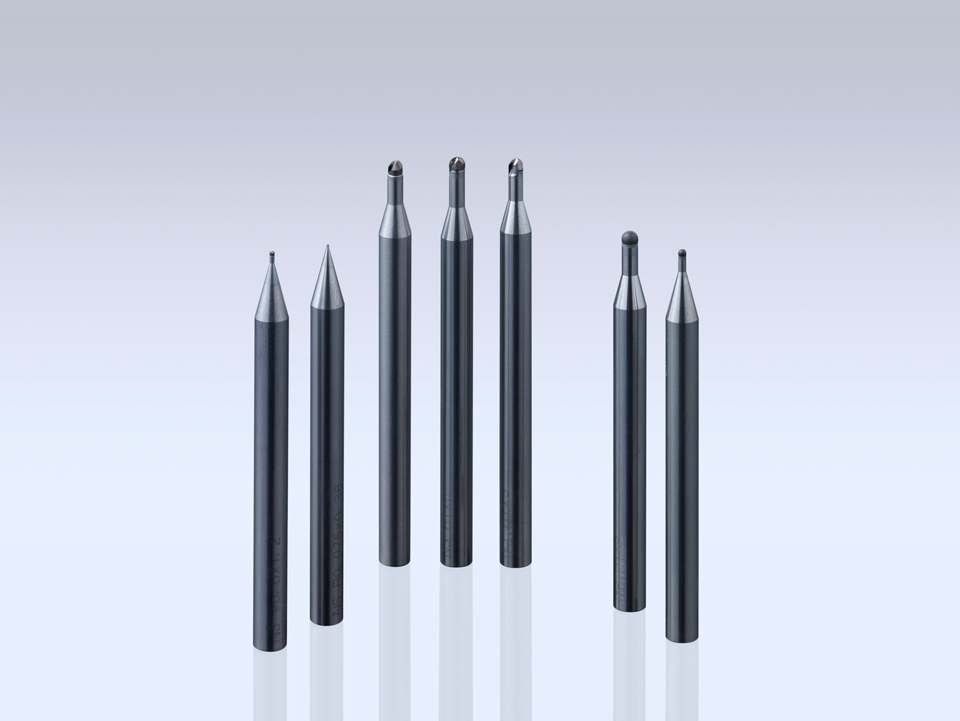
――「超硬小径エンドミル」に特化するきっかけは、いつ、何から始まったのでしょうか。
後藤:小径のエンドミルに特化し始めたのは、93年ごろからです。当時、家電や通信機などのデジタル機器が「軽薄短小」の方向に向かっていたことが理由のひとつです。外装が小さく薄くなれば、内部の部品も縮小しなければならず、製造現場ではそれらを加工するための工具が必要になると考えたのです。そして経営資源を他社が手がけていなかった超硬小径エンドミルに集約させる「ニッチトップ戦略」を掲げました。
――取引先にはどのような業種が多いのでしょうか。また、どのような現場で必要とされ、どう使われているのでしょうか。
後藤:精密金型や精密部品が必要とされる企業が顧客の中心です。特にここ数年はスマートフォンが普及したことで小径エンドミルが活用される機会が増えています。というのもスマートフォンのカメラモジュールや電子部品、小型精密パーツ用の金型製作にはエンドミルが必要不可欠なのです。
同じように自動車分野でも、従来のインストルメントパネルやスイッチ、コネクターに加え、ADAS(先進運転支援システム)の進展や自動運転への取り組みから、従来よりも小型のパーツを作るための金型が必要になり、小径エンドミルの活用が増えています。
今後はEV(電気自動車)やFCV(燃料電池自動車)など従来よりも小型のパーツが多数必要な動力が増えることが予想されます。これらの動力源の製造では精密金型が製造されるはずです。そうなれば、超硬小径エンドミルの必要性はますます高まるでしょう。
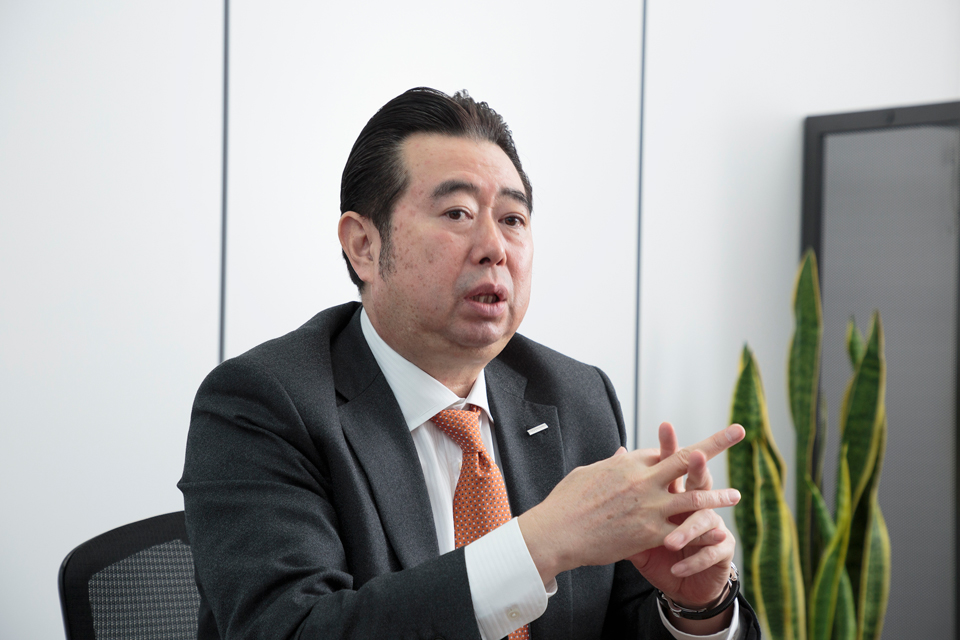
マンパワーとロボットを適切に使い分け、製品精度の向上と安定供給を実現
――「超硬小径エンドミル」の製造には、どのような難しさがあるのでしょうか。
後藤:エンドミルは切削によって摩耗していく消耗品ですが、個体差があったり、精度が低かったりすると、金型や部品を設計通りに切削するのが難しくなります。特に極小径のエンドミルの刃先は、目に見えないレベルの細さです。また、形状だけでなく回転の精度も高めていかないと、一部分は切削できるのに、ある部分は切削できないという不具合が生じてしまいます。
そこで重要になってくるのが、製造工程の監視と完成品の精度測定です。当社はJIS規格(日本産業規格)より厳しい自社基準を設けています。また、自社開発の工具研削盤(エンドミルを製造する機械)を使い、「全数自動測定器」で寸法を測ることで製造の安定性を確保しています。求められる精度がシビアなだけに、誤差をなくすため、製造工程での品質を細かく突きつめていくことが、私たちにはとても重要なのです。
――「超硬小径エンドミル」を製造する機械も自社開発されているのですね。
後藤:もともとは「超硬小径エンドミル」を製造できる工具切削盤が市販されていなかったことから始まりました。しかし、自社開発を進めたおかげで、製造現場に最も適切な機器類を設置できました。また、積極的なロボットの導入で製造工程の自動化も進めました。
製造の自動化はコストにも好影響を与えます。私たちが高品質の製品を市場の相場で販売できるのも、マンパワーとロボットを適切に使い分けて製造しているからなのです。
――品揃えや安定供給についてのお考えを教えてください。
後藤:当社の商品数は、1万点近くに上ります。そして、エンドミルは即納が鉄則です。納入が間に合わず金型や部品の製造が遅れては、お客様に迷惑をかけるからです。私たちは欠品を防ぐため、東京と仙台に加え、香港にも在庫を揃え、いつでも出荷できる体制を整えています。
過去には受注後に製造することもありましたが、それでは即納に対応できません。そこで、お客様のニーズをスピーディかつ徹底的に満たすため、在庫の管理方法を変えたのです。
これが幸いしたのが、2011年の東日本大震災のときです。工場復旧まで1カ月ほど生産が止まりましたが、在庫切れを起こさずに済みました。
2019年11月に竣工した新しい開発センターは、免震構造を取り入れ、震度7の揺れを震度4程度に抑えることが出来ます。また微少振動対策ダンパーにより、交通振動や建物内の設備機器等による微小振動をも抑える構造となっています。
未来を見越した提案や製品でユーザーの発想を刺激し、日本のものづくりに貢献
――先を見通して動くことは、御社の企業理念「『つくる』の先をつくる」にも通じるお話ですね。
後藤:ええ。私たちには、これまでになかった工具をご提案したり、高精度で安定した工具をご提供したりすることで、お客様の新しい技術や製品の開発に貢献したい。日本のものづくりを支えていきたいという強い思いがあります。
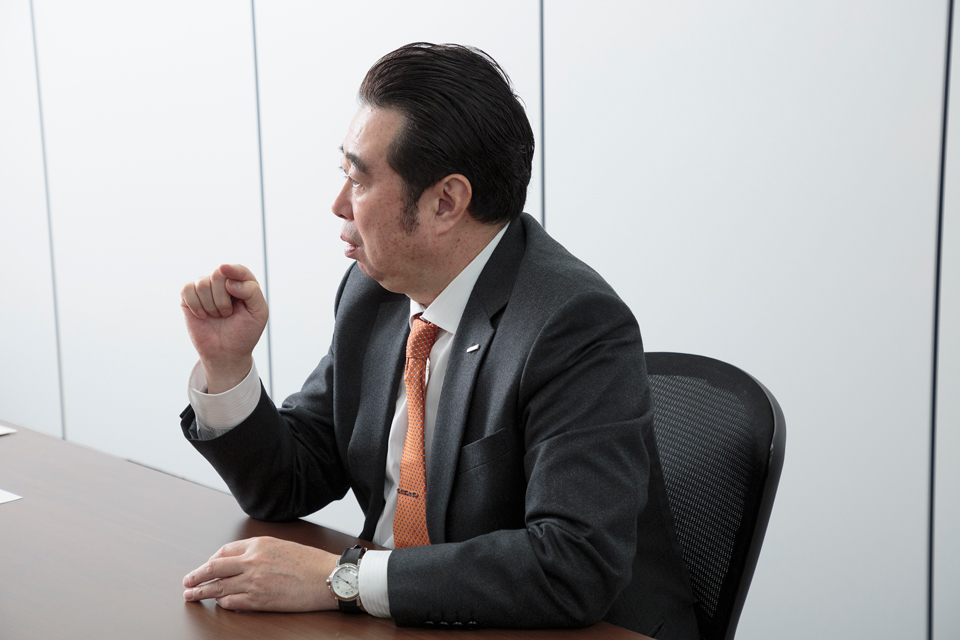
たとえば、「マクロエッジ」シリーズです。この0.1mm以下のエンドミルが生まれたきっかけは、お客様からの「0.1mm以下のエンドミルは作れないか?」という声でした。そして、0.03mmが完成したとき、そこで開発を止めてしまうのではなく、さらに0.01mmまで挑戦したことは、当社ならではの姿勢だと思います。
現在、最もよく使われている「超硬小径エンドミル」は1mmのものです。10年前は3mmが主流でしたから、必要とされるエンドミルはどんどん小径化しています。0.01mmのニーズは現状ほとんどありませんが、カタログへの掲載や展示会でお客様の目に触れる機会を増やすことが重要だと考えています。それにより、お客様の発想が刺激され、必要とする金型や部品が生まれる可能性が広がるからです。0.01mmのエンドミルが必要とされる未来も見越して製造することが、私たちの使命と考えています。
グローバル市場を切り拓くためのカギは「Made in Japan」
――超硬小径エンドミルは今後、どのような分野に広がる可能性がありますか。
後藤:考えている分野のひとつは医療です。医療機器も高度化・精密化し、いずれ軽量・小型化が課題になるだろうと予測しているからです。たとえば、胃カメラの検査が楽になったのは、パーツの小型化や精度向上があるからですよね。そのうちカメラやセンサーの入ったカプセルを飲めば、胃から腸まで丸ごと検査できる日が来るかもしれません。そんな未来の可能性を探ろうと、2月には、アメリカのアナハイムで開催された医療機器の展示会に出展しました。
――「超硬小径エンドミル」の将来について、どのような展望をお持ちでしょうか。
後藤:3Dプリンタの進化により、切削加工が不要になるとの見方があります。しかし、3Dプリンタが試作品や特注品といった1点ものの生産には効果的である一方、量産品を大量生産する場では、時間やコスト、精度の面でエンドミルを必要とする切削加工に取って代わることは難しいと考えています。
むしろ、超硬小径エンドミルの需要は、当面は拡大傾向が続くでしょう。2020年から本格的に始まる5G(第5世代移動通信システム)のサービス開始を筆頭に、CASEやMaaSの進展、IoTによるビッグデータの活用、AIの利用拡大、移動やコミュニケーション手段の変化、医療やエンターテイメントの拡大など、様々な分野で今後も小さく高性能な電子部品やIC、メモリーなどの半導体が膨大に必要となります。精密・微細加工のニーズが増えれば、付随して超硬小径エンドミルの需要環境も広がるはずです。
【用語解説】
CASE
Connected(コネクティッド)、Autonomous(自動運転)、Shared(シェアリング)、Electric(電動化)の頭文字を取った造語。今後の自動車業界の動向を示すキーワードと言われている。
MaaS
Mobility as a Serviceの頭文字を取った造語。ICTの活用により自家用車以外のすべての交通手段による移動(モビリティー)を1つのサービスとして捉える次世代交通システムの概念。
――御社は「Made in Japan」にこだわり、国内生産を続けています。日本の製造業が世界で活躍するには、これから何が必要とお考えですか。
後藤:「Made in Japan」は、当社にとって製品品質と生産効率を高次元で両立できる最もよい方法だと考えています。確かに人件費の課題はありますが、製造のオートメーション化を推進することで、1人当たりの生産量の向上は図れます。
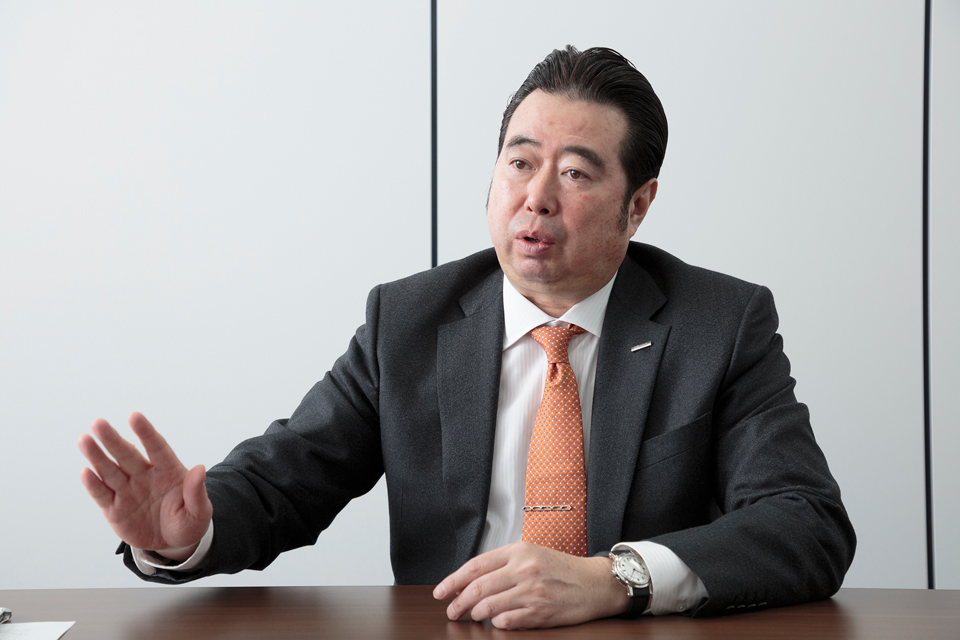
海外ブランドとの競合についても、当社の特徴である製品精度の安定性と供給の安定性が差別化の要因になります。自分たちのやり方で自分たちの技術を磨き、理想とするエンドミルを日本の工場から安定供給する。「Made in Japan」こそが日本のものづくりを支え、世界に臨む最適の戦略と確信しています。
日本人は他国の人々と比較すると、粘り強く研究し、試行錯誤しながら成功を目指すことが得意です。自分たちの強みと課題をしっかりと分析し、根気強さを生かせる分野を開拓することが、これからの日本には必要なのではないでしょうか。
私は、そのひとつが精密・微細加工だと思っています。精度の高いものづくりはまだ圧倒的に日本メーカーに強みがあるなか、電子機器の組み立てなどは海外拠点でもできますが、大切な技術開発は国内でやっているケースがほとんどです。医療機器への進出もその一環ですが、世界が求める精密・微細加工をすべて日本に呼び込むことはできないか、と考えています。そのために世界に向けて、日本にはこんな超硬小径エンドミルを製造する企業があるとアピールしていきたいと思っているのです。
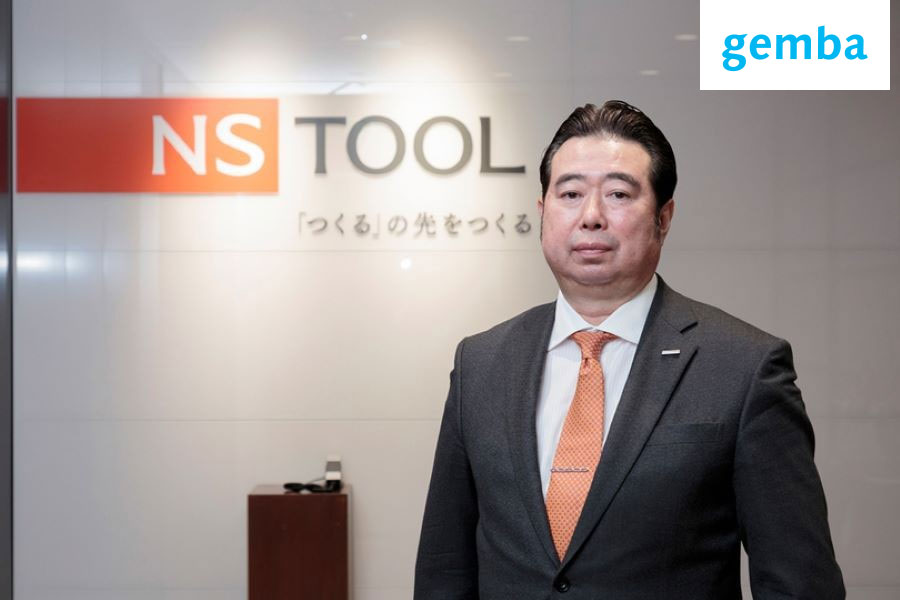