パナソニックが取り組む「現場プロセスイノベーション(GPI)」は、製造、物流、流通などサプライチェーン領域をはじめとした各現場におけるソリューション提供事業である。事業開始から3年目を迎え、サプライチェーンの自律化に向けた、ソリューションの研究開発に力を入れている。「自律化のカギになるのは製造業で培った“インダストリアルエンジニアリング”」だと語るパナソニック コネクティッドソリューションズ社 現場プロセス本部の一力知一(いちりき ともかず)氏に話を聞いた。
一力 知一(いちりき ともかず)
パナソニック株式会社 コネクティッドソリューションズ社 現場プロセス本部 エグゼクティブコンサルタント エバンジェリスト
1999年、松下電器産業株式会社(現パナソニック)に入社。データベースシステム開発、製造系基幹システム導入PJ、経営企画、IoTによるスマートファクトリー・スマート倉庫構築などに従事し、現在は社内で実践したオペレーションの知見とパナソニックのデジタル技術を組みわせた「インダストリアルエンジニアリング(IE)とDXの融合による経営オペレーション変革」を中核とするデータ駆動型経営オペレーション構築のコンサルタントとして、社外の製造、物流、流通業界における経営プロセス変革を推進。
モノづくりのマネジメント手法を、物流・流通業界にも役に立てたい
――まずは、一力さんの現在のミッションとこれまでのキャリアについて教えてください。
一力:現在は現場プロセスイノベーション事業の推進に加え、パナソニックの最新技術や事業構想を発信するエバンジェリストという役割で活動しています。
私はもともとソフトウェアエンジニアとして、松下電器時代の99年に入社しました。当初、担当したのは検索エンジンの開発です。その頃、Yahoo!をはじめ、一般の方々も日常的に検索システムを利用するようになっていましたが、日本語の検索精度はまだ未熟なものでした。当時、より精度の高い日本語検索エンジンのシステムを開発しようと、日々試行錯誤していたことを覚えています。
その後、自社工場に製造系基幹システムを導入する担当となり、システムの入れ替えを進めていたのですが、トラブル続きでなかなかうまくいっていませんでした。トラブル解決のための応援要員として派遣されたわけですが、そこではじめて基幹システムが実際にどう動くのか、工場設備はどのように稼働するのか、生産管理はどうやって行うのか、デマンドと生産計画はどう連動されるのかなど、モノづくりの現場を見ることができました。このときの経験は、今、現場プロセスイノベーション事業を推進するうえで大いに役に立っています。
そして2年がかりで基幹システムの移行が完了すると、今度は経営企画部へ。ここで経営戦略に携わるようになって、2015年頃からはIoTやロボットを活用して自社工場の改革を主導する立場になりました。ちょうど「インダストリー4.0」や「スマートファクトリー」といったコンセプトが各国で注目されるようになった頃の話で、「パナソニックもグローバルスタンダードに乗り遅れないように、インダストリー4.0に挑戦すべき」となったわけです。
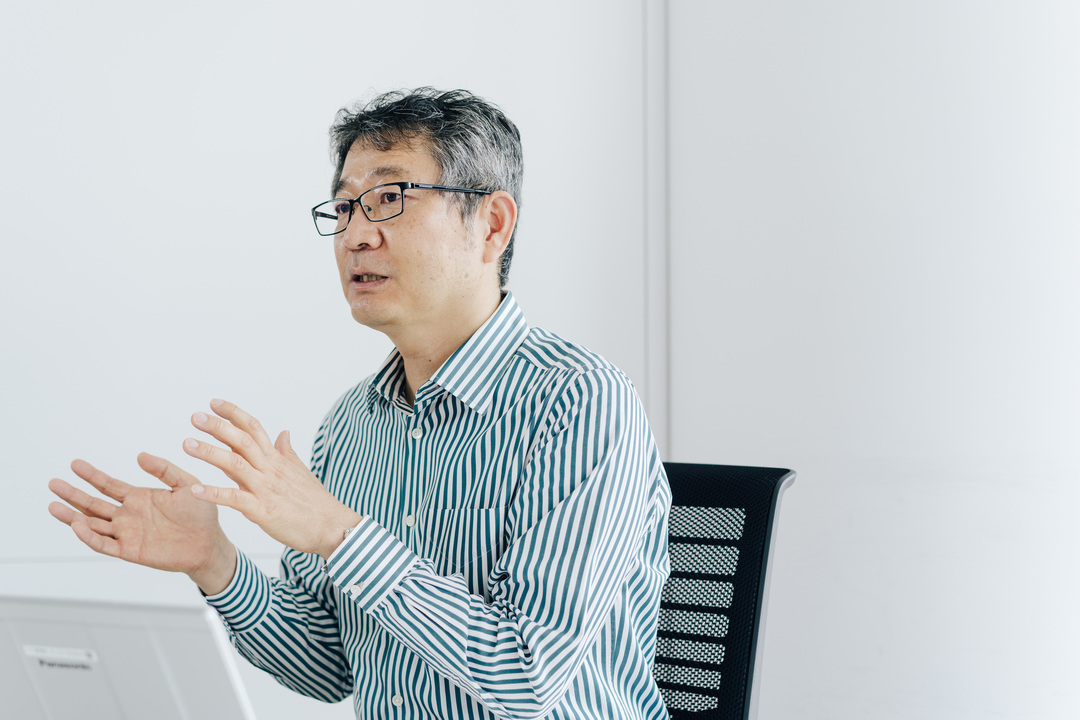
――以前、GEMBAでも、一力さんが携わられた佐賀工場のスマートファクトリー化の取り組みを取材させていただきました。
一力:ええ、あのように自社工場のDXや現場の作業プロセスの改善に取り組んでいたところ、取引先の企業様からもさまざまな現場の課題解決の相談を受けるようになったんですね。そこで2018年に現場プロセスイノベーションの国内事業を立ち上げ、製造・物流・流通といったサプライチェーン領域のお困りごと解決のためのソリューション提供をスタートしました。パナソニックの現場プロセスイノベーションは、このように始まったのです。
――しかし、家電メーカーとして成長してきたパナソニックが、なぜ物流や流通といった製造以外の領域でソリューションを提供できるのでしょうか。
一力:国内外にいくつもの生産拠点をもつパナソニックには、インダストリアルエンジニアリング(IE)の知見が蓄積されています。IEは、業務プロセスを標準化し、現場のオペレーションを定量的・科学的に分析することで業務効率および経営効率を最大化する技術です。パナソニックでは長年にわたり、モノづくりの現場で繰り返し実践してきました。
そして、パナソニックが強みとするセンシングやAI画像認識などのデジタル技術とIEを組み合わせることで、製造業界だけでなく、その近接領域である物流・流通業界の課題解決に貢献できそうだということがわかってきました。
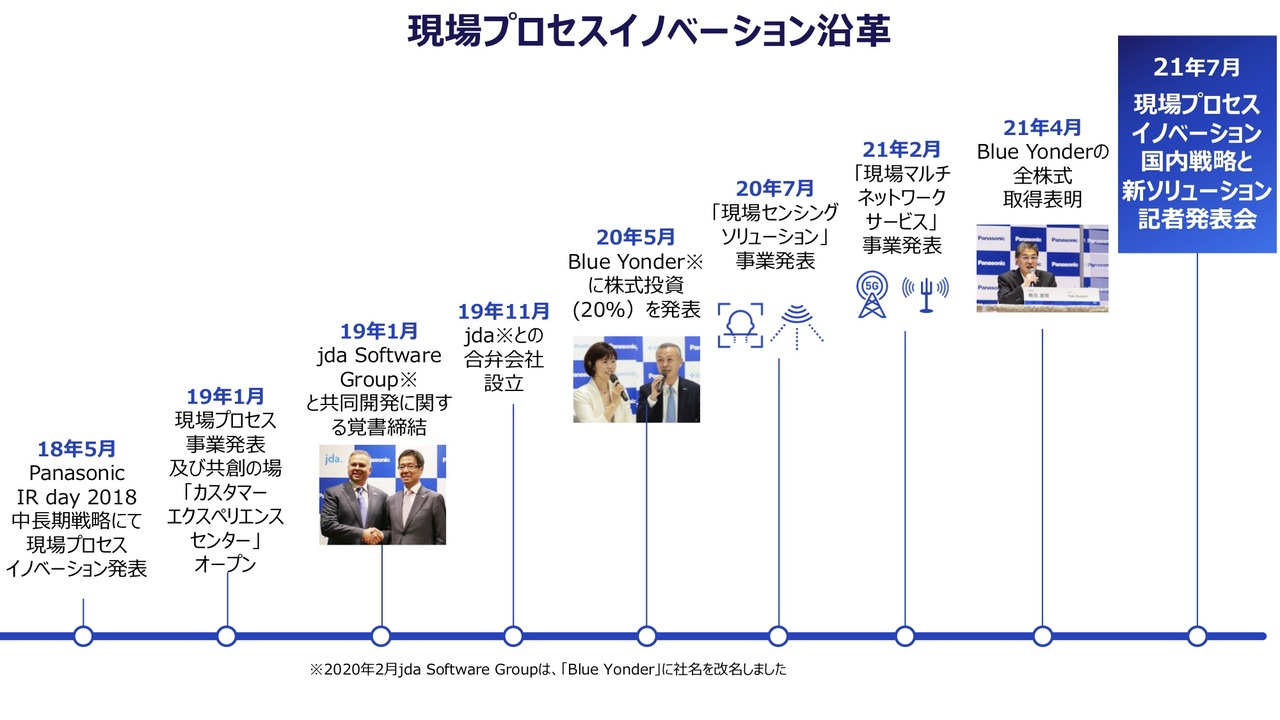
一力:ここ数年、物流領域を持つさまざまなお客様からご相談を受けています。物流領域において、人手・トラックの不足といった課題はこれまでもありましたが、コロナが1つの契機となりそれらがより深刻化しています。これは、サプライチェーンにおける物流の位置づけが今までと比べものにならないくらい重要になってきたという変化でもあると考えています。
この機に改革を行おうとしたときに、定量的なデータや基準がないために、経験と感覚による判断からなかなか抜け出せないことが多いです。実際、IEおよびデジタル技術で可視化をしてみると、現場の感覚に反して、業務量に対する人やトラックなどの数はかなり多いということがわかってきます。多いときで3倍程度過剰だったこともありました。つまり人が不足しているのではなく、人手不足「感」であったことがわかります。
つまり、業務プロセスが標準化されていないために、待ったり迷ったりという非付加価値作業が増えて荷物がうまく流れず、次の工程の人達を待たせてしまっているケースが多いということだったんです。IEでいうボトルネック(流れを悪くする要素)がいたるところで発生をしていたのです。業務プロセスを標準化し、それらを解消することで業務効率は大きく上がりました。
現場プロセスイノベーションの第一歩は、「可視化」です。可視化することで課題の「真因」が明確になり、ボトルネックを見つけ出し、具体的な解決策を講じることができるようになります。
目指すのは「自律神経」のようなサプライチェーン
――では、あらためて現場プロセス事業で目指す「自律的なサプライチェーン」がどういうものか教えてください。
一力:ごく簡単にいうと、人体のように自律機能を備えたサプライチェーンです。
人間の身体には、内臓の動きや血液の流れをコントロールする「自律神経」があります。この自律神経の働きによって、私たちの心臓は自ら動き続け、体温が調整され、血液が全身に運ばれることによって酸素が供給され生命が維持されているわけです。
先日、体調を崩したことがあったのですが、身体がそれ以上悪くならないように、発熱というアラームを出し、全体の機能をスローダウンさせる一方、酸素供給量を増やすために心臓の動きだけは可動率をあげ、回復させるという働きが自動でなされました。言い換えると、自律とは個別個別の機能が勝手に動いていても、もしくは動くことで、全体最適がなされている状態を言います。
この「人体」を「サプライチェーン」に置き換えて考えてみてください。造る、運ぶ、売るという機能が個別個別に動いても全体最適がなされる状況です。具体的には、店舗に必要なものが必要なときに必要な量だけあるようにするという最適な状況を物流、製造が柔軟に変化を吸収して、実行できる仕組みです。
今、店舗に何が必要で、何を造れば、何を運べば良いかをタイムリーに検知し、製造・物流プロセスで独自に判断し、必要に応じて対応を変化させることが次世代の全体最適だと考えています。そのことにより、チャンスロスや廃棄ロスなどムダを多く減らせると思います。
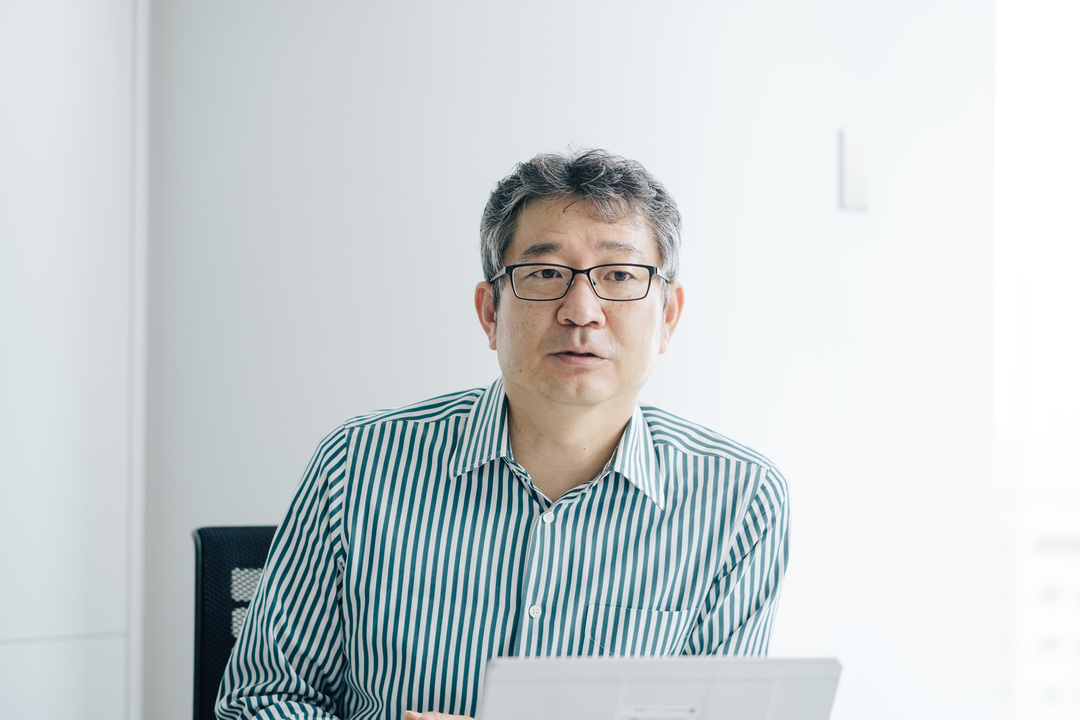
――たしかに、サプライチェーンが自律化されると、多くのムダを大きく減らしてくれそうですね。
一力:ええ、そうですね。ただ、サプライチェーン自律化の実現はそう簡単ではなく、その途中にはいくつかの段階があります。第一段階は、先ほどお話した「可視化」です。現場の状況をデータ(数値)として収集します。
次は、そのデータを活用するために「標準化」が必要です。「標準化」とは個々の業務における標準値(作業時間や生産性やコストなど)を定めることを指します。そのことにより、データから良し悪しや課題がわかります。つまりデータを意味のある情報に変えることで、初めて活用できるのです。業務プロセスの変革には、標準値、つまり基準をつくることが必要不可欠と考えています。
そして、この標準値と実績値のギャップをゼロにすることが「最適化」です。「自律化」はその先にあり、業務プロセスの標準化がどんどん進み、AIなどのアシストを受けながらデータを情報に変えて活用が進むことで実現します。「可視化」「標準化」「最適化」。この3つを経てようやく「自律化」にたどり着くことができると考えています。
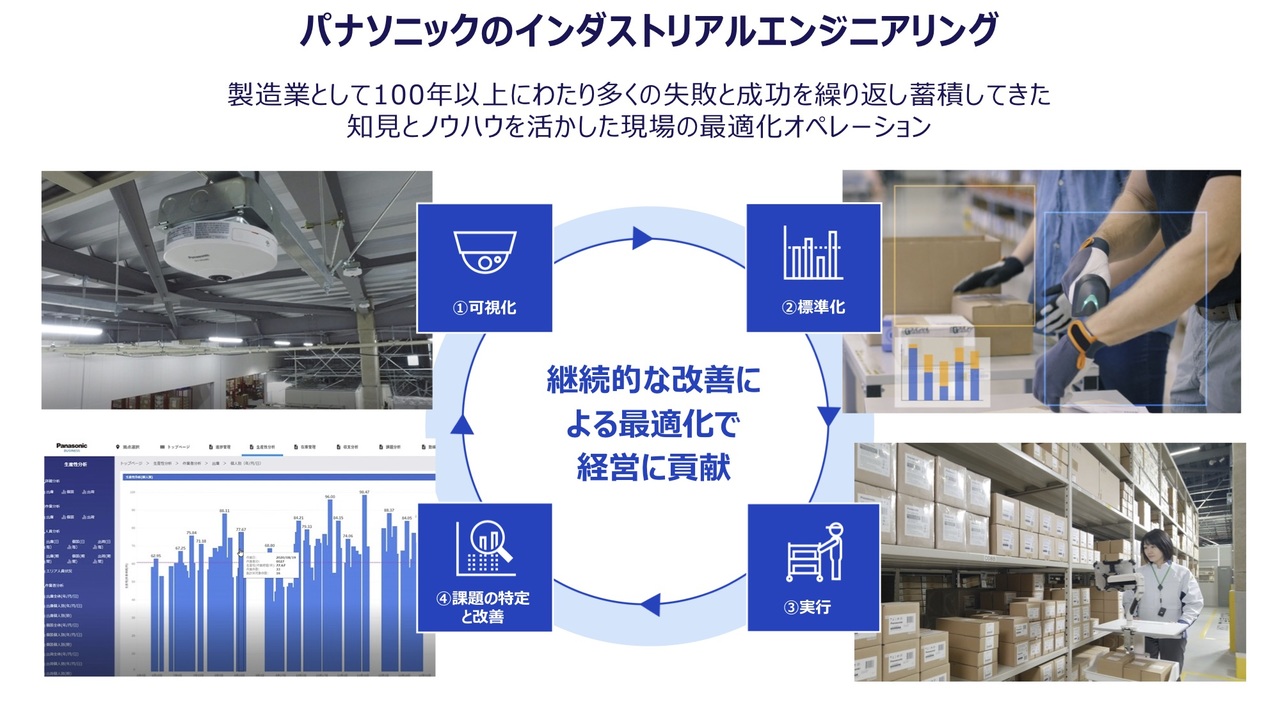
一力:この一連のプロセスをインダストリアルエンジニアリング(IE)と呼んでいます。これこそが、サプライチェーンの地上・低空領域におけるパナソニックの強みでありノウハウなのです。
このたび発表させていただきました「現場最適化ソリューション」とは、このIEの知見により、お客様の業務プロセスを改善し、現場を最適化するためのソリューションです。
――あらゆる分野でサプライチェーンの自律化が実現すれば、私たちの生活や社会の仕組みが大きく変わりそうですね。
一力:ええ、社会課題の解決にも貢献できると思っています。その中における重要なテーマが持続可能な社会をつくるということです。近年、地球温暖化など環境問題への取り組みが待ったなしの状況です。サプライチェーン上のムダの削減は、不必要なCO2排出を削減することにつながると考えています。
例えば、物流機能の強化によって、発注してから店舗に納品されるまでの期間が短縮されれば、売れるタイミングに商品を届けることができ、廃棄ロスを削減できます。廃棄は生産や配送において全く必要なかったCO2を発生させたことになり、廃棄ロス削減がCO2削減にもつながります。
また、CO2排出量に直接影響のあるトラック積載率は現状約40%※まで低下しているといわれています(※国土交通省「自動車統計輸送年報」より)。もし物流が最適化されることで積載率が50%向上して90%になれば、現在トラックから排出されているCO2を半減させたことに相当するのです。
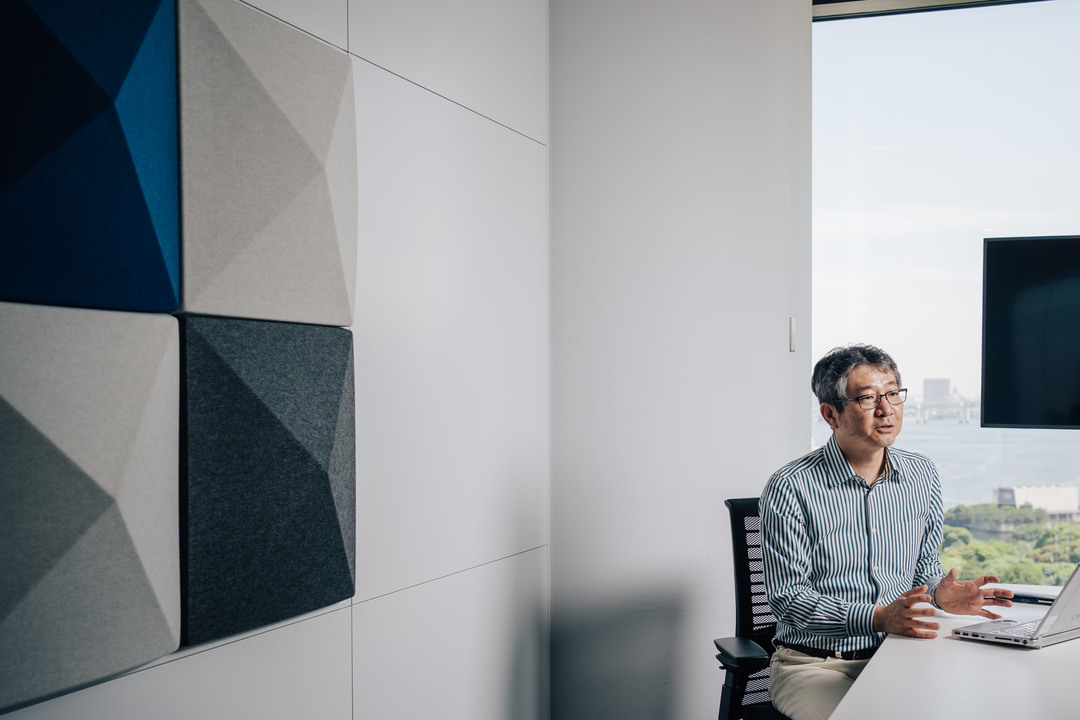
――現場プロセスイノベーションは、社会課題の解決も見据えているんですね。
一力:はい。パナソニックには「産業人たるの本分に徹し、社会生活の改善と向上を図り、世界文化の進展に寄与せんことを期す」という創業以来の綱領があります。これを現代的にわかりやすく言い換えたのが、「A Better Life, A Better World」という経営理念です。
パナソニックは創業以来、「“より良いくらし”を追求し、拡げていくと共に、地球環境への貢献をはじめ、グローバルに“より良い世界”の実現に貢献していく」という思いで事業を推進してきました。
加えて、社会課題の解決に向き合っていくことで、パナソニックが今後の100年も世の中に貢献できる企業であり続けたいと考えています。そういう意味で「現場プロセスイノベーション」は、パナソニックという企業が社会の公器として存在し続ける意義を示すものだと思っております。
これからも、製造、物流、流通などサプライチェーンに関わる分野でさまざまな社会課題の解決につなげていきたいと考えています。
――最後に今後の展望について教えてください。
一力:最終目標はやはり自律的なサプライチェーンの構築への貢献ですが、まずはIEとデジタル技術を融合した可視化・標準化・最適化によるDXをとおして、現場の競争力強化および現場と経営が同期した経営マネジメントを実現することです。
経営層は、営業利益や売上という指標で経営力をみて、現場のマネジメント層は市場競争力や事業競争力を原価という指標でみています。他社に比べて勝っているのか、お客様の求めているものに対して適切にアプローチできているかといった視点です。そして現場は文字通り現場力であり、タクトや稼働率、可動率といった指標で見ています。
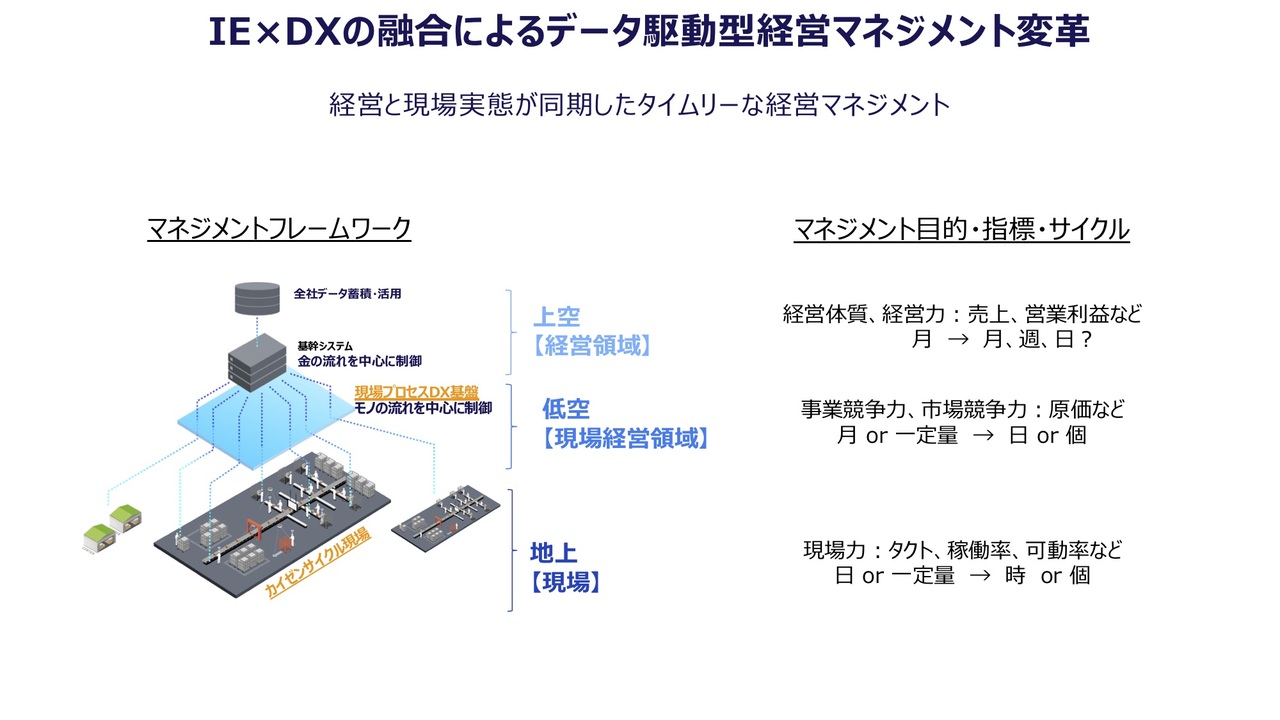
一力:経営層と現場のマネジメントは、情報の粒度と単位が違うのでなかなかつなぐことは難しいです。お金を単位にして最適化していく経営と、人とモノと情報の単位で最適化していく現場。その2つを同期させ、変換しながらつなげていくことで、現場の競争力が経営力に直結すると考えています。
これは、パナソニックが製造業として100年間培ってきた可視化、標準化、最適化という考えを実装した経営マネジメントです。
サプライチェーンを構成する製造、物流、流通は、社会において必要不可欠な存在であり、日本が誇りを持っている領域です。IEとデジタル技術の融合によるDXの実現をとおして、人がより付加価値の高い業務に集中することで競争力をさらに高め、仕事の魅力がどんどん増すように、微力ながら業界全体に貢献していきたいと考えています。
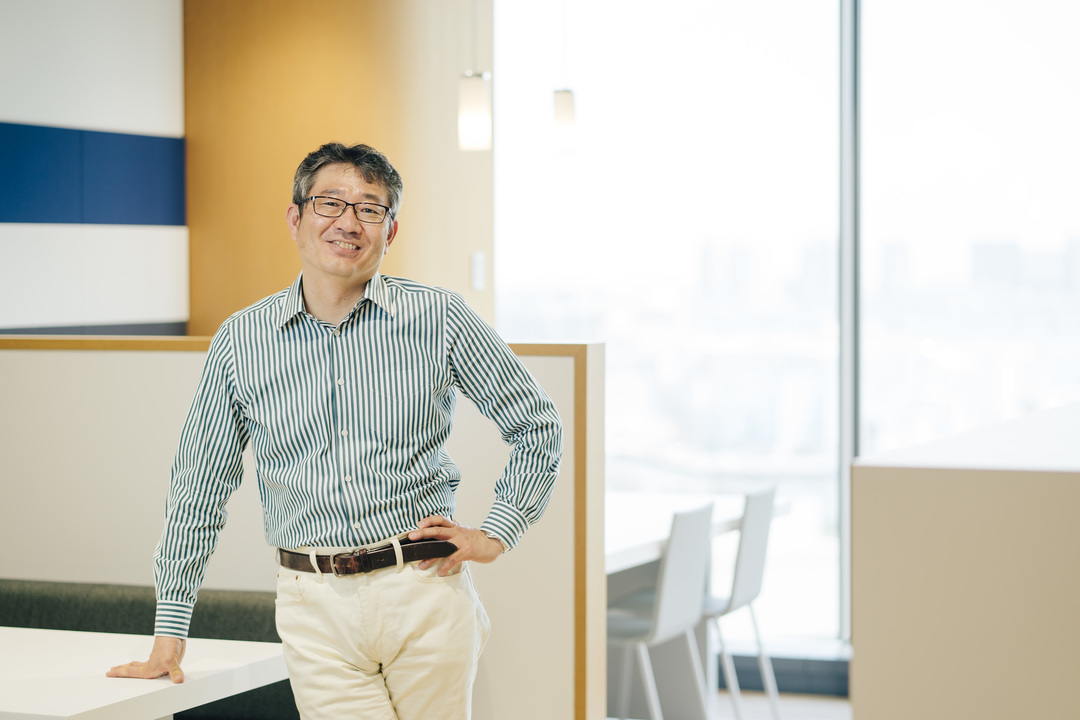
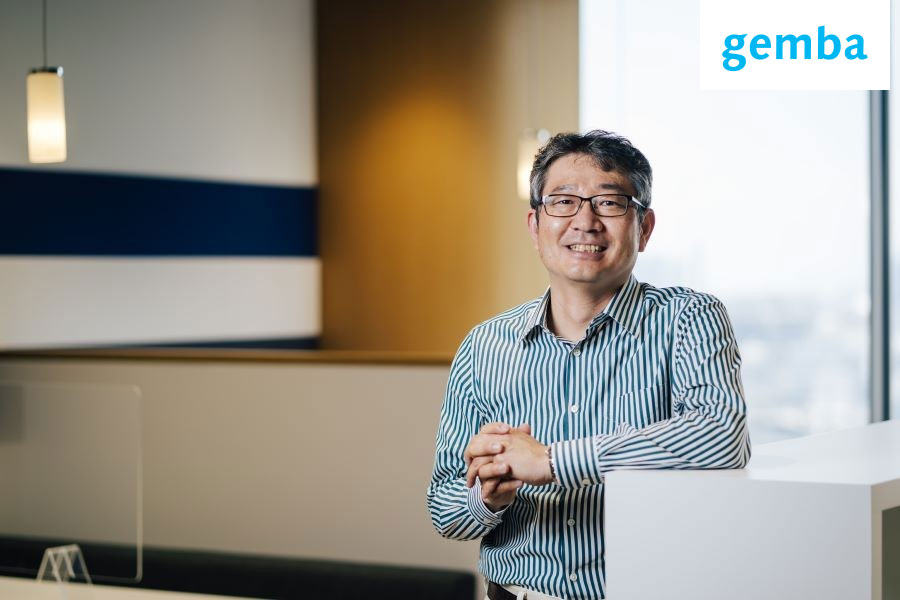